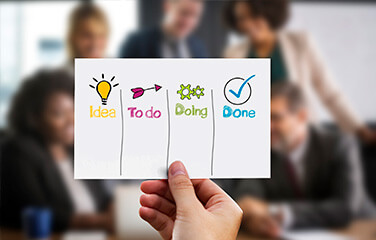
Kanban, despite not being considered an agile methodology, is a powerful tool to help improve the organization of tasks, which tend to directly impact performance and income. It is understood as a pull system, where, to execute a new activity, a previous one must be completed, in order to release the flow.
Origin of Kanban
This method originated in Japan and emerged from Lean thinking, which aims at continuous improvement focused on processes, being more open to adaptation, allowing for a pilot implementation that evolves, as more is learned about it and put to use. act and synergy with your workflow, ensuring more agility and predictability, which allows for greater risk management, in addition to there being less resistance from the team in working in these ways, since it is not rigid.
Getting started on the Kanban journey
To start using Kanban, we must first map the workflow, understand where execution begins and where it ends. This way, we can create a framework that encompasses all phases. The next step, then, is to list all the tasks that must be completed in this framework, taking into account the number of professionals who work in each part of its development. Thus, if there are two employees assigned to the testing area, there cannot be more than two cards released at this stage of the table, unless it is an emergency, cases considered exceptions, which must not be more than one and which must respect a policy express urgent cases to ensure that it is not exceeded at all times.
This is necessary, as Kanban works with a WIP limitation (work in progress, or, in Portuguese, work in progress), defined by the workflow, like a queue, only starting a new activity, when a task is completed. previously designated in the table.
It is important to remember that Kanban requires you to seek to understand what stage your development is at before making changes, in addition to functioning as process management, not areas or people, and the professionals involved must feel comfortable so that they are engaged. in facing the necessary changes so that your company’s Kanban model gets off the ground.
There are some types of Kanban that are more suitable for application when you do not yet have something structured and a team engaged in applying continuous improvements, always remembering that you must start slowly, one step at a time, in order to guarantee the successful implementation of the method throughout its production process.
In short, applying Kanban in a production process means bringing everything that is happening to everything and everyone into the field of vision, clarifying the flow of services, the delivery time of each individual, imposing a limit on the work in progress, so that more activities are not started than are completed, impacting a continuous flow of work completion.
Fundamental Concepts
Implementing the Kanban system in your company requires some theoretical knowledge to help you make better use of everything this framework offers in terms of process improvements.
Kanban allows you to visualize three main points: lead time, which is the time it takes the team to complete an activity, from one end of the board to the other; cycle time, understood as the completion time between one stage and the next; and the trhoughput, understood as the flow of activities, determined by how many items the team can complete in a period of time.
It is important to highlight that the success of applying Kanban in a work team also depends on not making mistakes, such as moving a task backwards on the board, activities are never retroactive, they always go from left to right, following the workflow , just as a field should not be created for activities that are prevented from continuing, they remain on the board until they are completed. Not applying a limit to execution or imposing metrics on the team can negatively impact implementation, in the same way as punishing or rewarding them based on this data.
Queuing theory explains how the workflow works, knowing it, it is possible to have a reduction in waiting time and speed in the time it takes to complete a task, which impacts a better use of available services. Queues are nothing more than a cluster of requests (services) made by customers, waiting to be fulfilled, while a system is the sum of the queue and services.
A Kanban system seeks to solve the waiting time of these queues, bringing, in a continuous improvement scheme, to visually demonstrate where the production bottlenecks are, which require more time than necessary to be completed. To do this, it uses some tools such as CFD charts (Cumulative Flow Diagram) where it is possible to understand, according to the curve presented, where the loss point of that process is located.
To measure how your company’s Kanban model is progressing, it is important to focus on the cadences, which can be understood as meetings and cyclical reviews that aim to evaluate and drive gradual changes to achieve effective service delivery, this increases the predictability of the process. productive, in addition to improving feedback from all areas involved, increasing the focus on productivity, action, engagement and commitment from everyone.
Applying Kanban with tools
To get started with Kanban in your projects, there are some online tools that aim to offer a board model with the steps of your workflow.
Gipo is an extremely suitable tool to start venturing into the world of Kanban. In it, you can define steps according to the work format and size of the team that will work.
During workspace creation, which resembles Kanban boards, standard steps such as “Pending”, “In progress” and “Finished”, but are not limited to that! You can include as many steps as necessary, and you can also define the number of tasks to be performed per step, applying the WIP concept.
And most importantly! The tool doesn’t leave you stuck! As your workflow takes shape and changes, you can create or delete steps where task cards will move.
[…] bem como em que etapa do processo cada uma delas se encontra. Isso é possível através de um quadro kanban visual e […]
[…] kanban focuses on the production flow of your project. It makes processes more visual and simple to […]